Once complex and very expensive restorations such as the Woreley (also know as the Paulo Malo bridge) are now incredibly cost effective due to modern CAD/CAM technology. This type of bridge is simply a full arch implant structure that caries individual crowns.
So before we look at this case in detail we will cover how new technology has changed this and made the individual crown bridge (ICB) a much more attractive option for restoring a full arch.
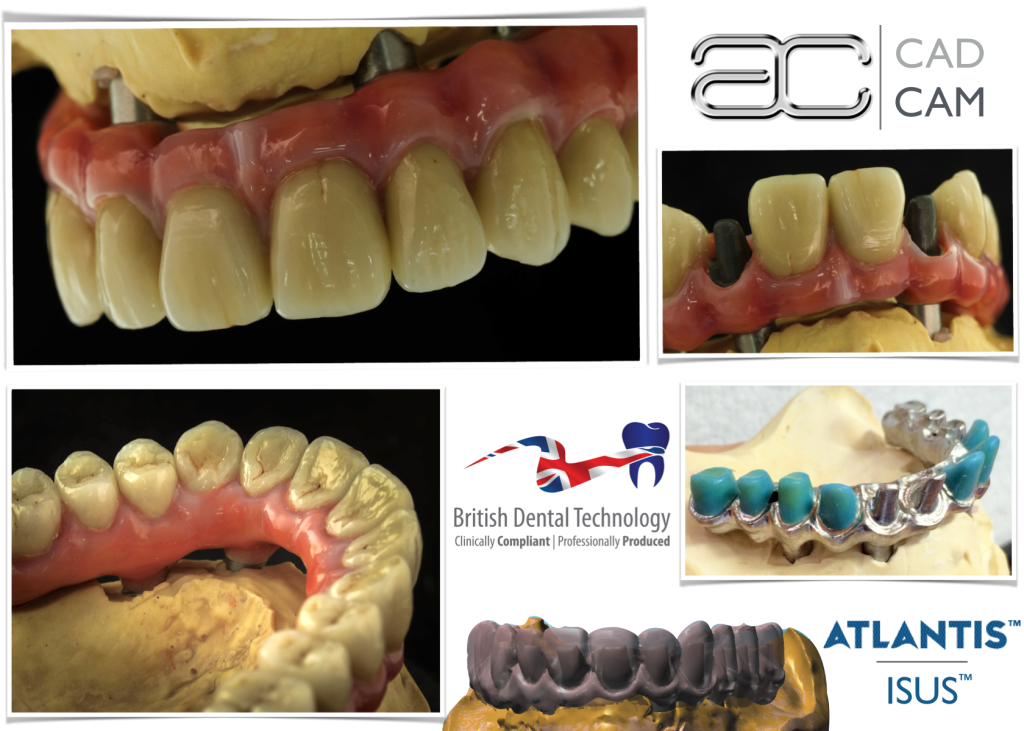
Cost Efficiency
The quality and stability is the primary driver, with the cost efficiency also being a fantastic bonus brought about by the time saving made when a lab switches to a truly digital workflow. Add to this that we do not have to buy expensive implant components or alloy to cast the restoration and there is a significant cost saving to be made, without compromising quality. In fact quite the opposite.
By incorporating new technology we are able to exactly copy the patient approved setup and ensure our designs will be right for the final restoration. One of the most important factors is that we can check these designs and flag up any issues and discuss the best plan of action in the CAD state, before any financial commitment has been made to producing a structure.
Unmatched precision
Thanks to the CAD/CAM technology and our partnerships with world leading milling centres that specialize in the producing structures of the highest quality to the tolerances required for aerospace, medical sector and research projects such as the CERN Large Hadron Collider. Using the skill and experience of these long established partners we are able to deliver a wide range of implant options with incredibly cost effective pricing, which crucially have unparalleled accuracy, stability and passivity of fit.
CAD/CAM milled titanium or chrome frameworks are incredibly strong and stable which provides the ideal sub structure for your large span restorations, furthermore we have years of clinical trials that show us these structures perform incredibly well. They are tried and tested.
Because titanium and chrome CAD/CAM implant frameworks are milled from a solid homogenous block of material there are no casting stresses, voids or porosity within the framework which could lead to hygiene problems if against the tissue, or even failure of the whole restoration in the future.
This is the very foundation of our work so it is vital that we can guarantee that these are completely free of any flaws which may lead to future complications or even failure. We focus on the quality and integrity of the CAD/CAM structure above all else, which is why we only work with milling partners who will guarantee their structures against failure if we stay within their design protocols.
Why use a CAD/CAM implant Individual Crown Bridge? (ICB)
Now that technology has made this restorative option far more cost effective and predictable, it’s perhaps a great time to benefit from the unique advantages that the ICB can bring to a full arch implant restoration.
What’s different on an ICB to a traditional screw retained bridge?
Diversity
Effectively the ICB is just a platform for 12 individual crowns, which means we are liberated to use whichever material we feel is best for any particular region of the mouth. Why be locked to just one material for the whole restorative arch when we can take our pick of the best material for each quadrant?
We may want to benefit from the shock absorbency, fracture resistance and enamel matched tooth wear that we can get from the new Hybrid Nano Ceramic materials such as Vita Enamic, which have been engineered to offer an improved restorative solution to many of the traditional materials on the market today. Or perhaps even the absolute strength of a full zirconia crown making these the ideal restorative material for molar teeth, especially in patient with a history of breaking molar teeth/restorations?
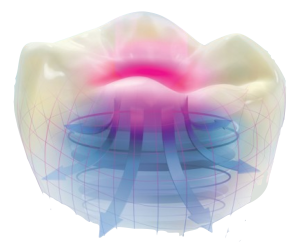
We have information on both these options
here.
However in the anterior region a patient will most likely want to have the very best aesthetics possible, a result that is only really achieved by working with a highly skilled ceramist using either pressed ceramics, ceramic layered on zirconia or time proven porcelain fused to metal.
The advantage is that with an ICB we are free to mix and match our restorative materials on the same arch and restore each case specifically to each patient’s unique requirements.
Maintainability
Because we have a base structure that is screwed onto the fixtures and then individual crowns made upon the structure it’s easy for the surgeon to repair or replace any of the individual restorations without having to remove the whole of the patients implant arch.Even if we needed to replace a whole crown (or number of crowns) many years down the line we can have an impression of the ‘prep’ and a new crown be made at the lab while the restoration as a whole remains in the patients mouth, which is not the case for a full arch screw retained restoration.
As with our Visio.lign implant structures the key is to ensure we are offering a clinical benefit over traditional restorative implant solutions.
Rather than layer pink ceramic onto a chrome framework which may crack and would need to be re fired in a furnace to restore to it’s original state at some point, we prefer to make the CAD/CAM milled substructure out of titanium and layer Crea.lign composite onto it, which means that it is easy to repair and maintain should any of the gumwork in situ should it need this in future.
We choose crea.lign composite because it is shown to resist plaque adhesion and staining to a very high level, similar to ceramic as show in the table below.
This also allows us to do a whole refurbishment of the structure many years down the line if needed, all without the structure ever needing to be exposed to the heat and stresses of a porcelain furnace.
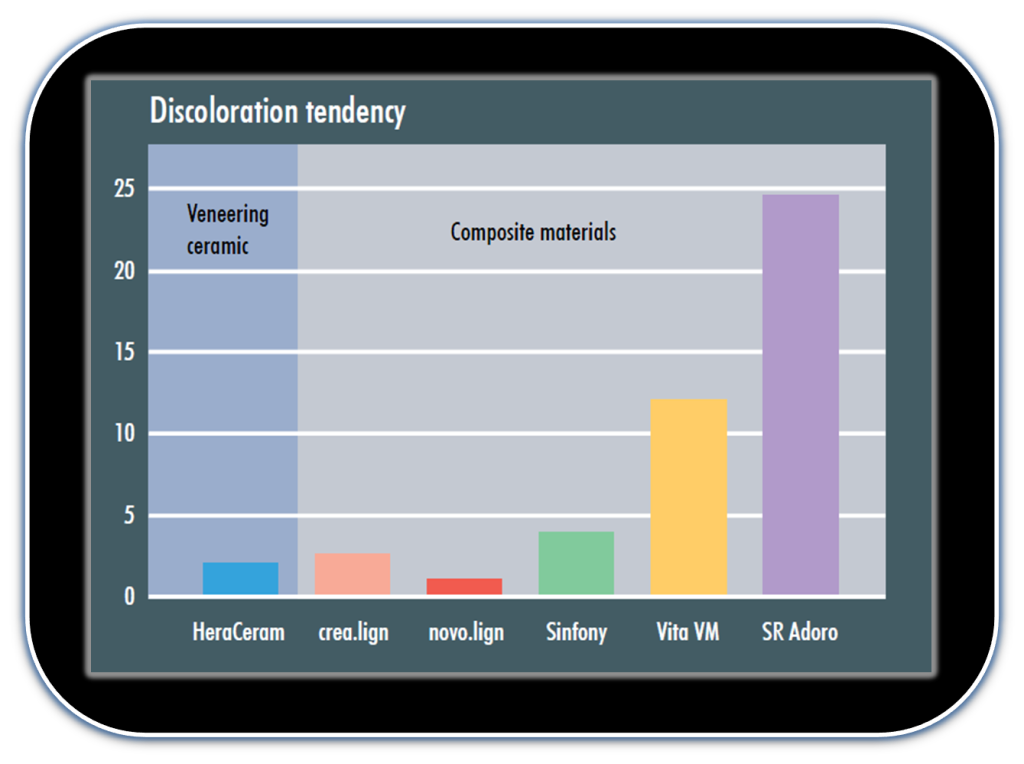
Average tendency to discoloration of composite materials compared to HeraCeram ceramic after storage in coffee, tea, tobacco, red wine and methylene blue.
Research report from the university of Jena on material testing of
veneering materials, July 15, 2010, by Dr. A. Rzanny and Dr. R. Göbel
Aesthetics
Using an ICB style implant bridge we will conceal the access holes in the primary structure, the final crowns do not need any access holes filling, which although not a particularly tricky problem for our experienced implant surgeons, it is still something we have to consider on a screw retained bridge such as the one shown below.
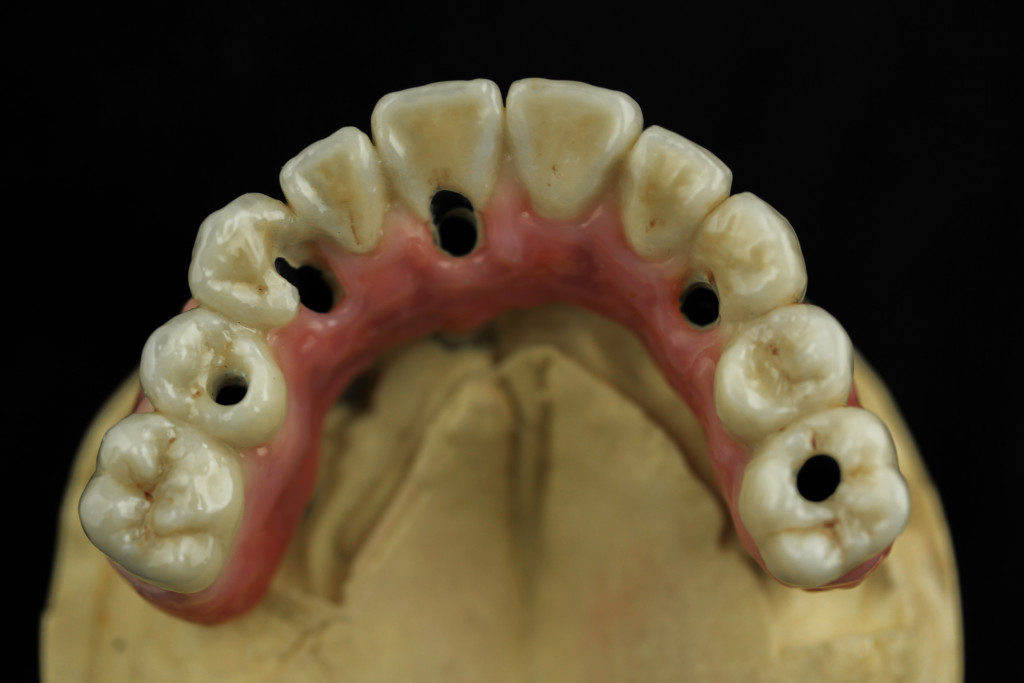
However using an ICB, it’s nowhere near as vital where the access holes of the structure will emerge as we can ensure they will never be coming through the aesthetic zone of our restorations.
To reduce surgery time we cement most of the crowns into place so that the surgeon only needs to cement the crowns that go over the access holes in the preps, this happens after the structure with all crowns on has been tried in and the surgeon and patient are happy. After this the final crowns that cover the access hole preps are cemented into place with a temp cement.
We can also engineer removal notches into the crowns to allow for easier removal should the surgeon ever want to access the screws again.
With a CADCAM milled ICB is a final result that looks just like a full arch of natural dentition, even when viewed from occlusally and palatally as shown below.
Crowns tried onto bridge and final occlusion checks carried out.
Final bridge fitted, which was an exact replication of a pre agreed tooth setup and tissue contour that the surgeon had taken quite a bit of time to perfect and agree upon with the patient at the trial stages. The lower was an acrylic bridge upon titanium framework whith the prosthetics by Egan Dental Laboratory.
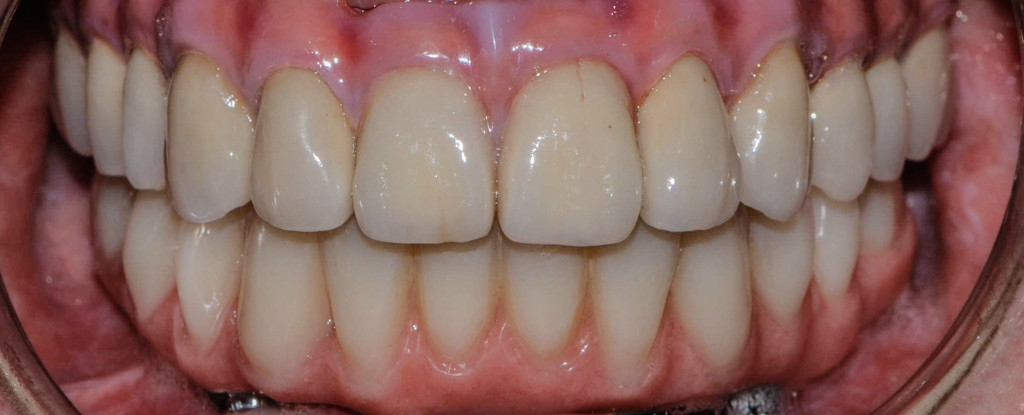
Not all CAD/CAM is the same
For us it was an obvious move to go from casting techniques to milled one piece structures as we were eliminating a high component and alloy costs to the surgeon, along with eliminating the inconsistencies and problems that are associated with cast implant structures. So there was both a financial and clinical benefit to the surgeon and patient by embracing this new technology, a true win/win situation.
These full arch restorations are by their very nature are a big financial commitment for the surgeon and patient even with the huge cost savings of CAD/CAM, and therefore should be designed to last our patient a very long time indeed, ensuring we have kept all potential failure risks to an absolute minimum.
We personally don’t want any question marks over the strength, stability or integrity of primary implant structure or material used on this type of ICB for our clients, which is why we only work with proven materials and market leading partners who are able to guarantee the structures they provide.
Our philosophy is to offer uncompromised solutions to our surgeons utilising the latest technology and ensuring maximum cost efficiency, but crucially without any compromise on quality or integrity of the restorations or materials used to provide them.
It may well be that we are best looking to evidence based solutions and cautiously integrating the newer materials into our restorations in areas where their failure will be easy and convenient to rectify without causing the patient to lose their dentition? As they prove themselves we will have the evidence of their success and confidence to use them more widely.
Why risk all the months of planning and implant integration for the sake of saving 96 hours on the very structure that will be the backbone of the final restoration for the patient, and will be subjected to high stresses over the many years it will serve the patient as a replacement to their lost dentition?
Will the patient thank us for saving 4 days while they are in temporary restorations if the final prosthesis causes them inconvenience, or in the worst case failure that requires them to go back to temporary restoration or denture while the final is remade?
Summary
Although there is no single ideal solution that covers all full arch implant restorations the recent improvements in efficiency by using CAD/CAM systems with clinically trialed and historically proven materials have made this type of ICB restoration a much more predictable, practical and affordable solution for our patients.
From our experience the key is using the right combination of materials in their appropriate place on the restoration. For example using the shock absorbing materials on the individual final restorations in the molar region where they are easily accessible and replaceable or repairable in situ. Helping to reduce inconvenience to patient and wasted chair time for the surgeon
As with our Visio.lign implant structures the thought process is to ensure we are offering a clinical benefit over traditional restorative implant solutions by offering materials and designs that give the surgeon easy ongoing maintenance and repair options for the patient. Maintenance is especially important on the full arch restorations, which we plan and expect to serve the patient for many years to come.
We have a world of materials and options at our disposal and always pass this onto our surgeons so that they can make an informed choice regarding the best restorative solution for their patients, many of those surgeons are now choosing the ICB type structure.